Jung-Hwan Park1, Seong-O. Choi2, Yong-Kyu Yoon2, Mark G. Allen1, and Mark R. Prausnitz3. (1) Georgia Institute of Technology, 311 Ferst Drive, Atlanta, GA 30332-0100, (2) Electrical and Computer Engineering, Georgia Institute of Technology, 311 Ferst Drive, Atlanta, GA 30332-0100, (3) Chemical and Biomolecular Engineering, Biomedical Engineering, Georgia Institute of Technology, 311 Ferst Drive, Atlanta, GA 30332-0100
Microelectromechanical system (MEMS) techniques have been developed to manufacture biomedical devices. Silicon-based fabrication processes have been used for this application because of its precision in engineering surfaces. However, a significant obstacle of the silicon-based processes is that they are high-priced processes for fabricating micro medical devices. Instead of photolithography typically used in silicon processing, the micromolding techniques have been developed to fabricate microstructures for low cost, ease of processing, and mass production potential. Poly di-methyl-siloxane (PDMS) has been used as a mold material for the fabrication of microdevices by micromolding because PDMS is durable, optically transparent, inexpensive, and moldable. Conventional micromolding methods using polymer melt provide rapid and low-cost ways to fabricate microstructures. However, the multi-compositions and multi-geometries of some microstructures make it very diificult to copy them from a mold when using a polymer melt, which contains a compound that may flow into the mold cavities at high temperature and high pressure conditions. In this study, polymer micro-particles encapsulating chemical compounds were used as the filling material for micromolding. The process of this new approach consists of filling polymeric micro-particles in the mold at room temperature and then melting or bonding particles using plastic welding methods. Three microneedle structures, with varying features, are presented in this study to demonstrate the capability of the particle-based micromolding process. First, multi-layered microneedles were fabricated, having varied composition in different parts of the microneedles. Second, a porous microstructure consisting of micro-particles partially welded together was made by ultrasonic-welding of micro-particles in the mold. Finally, arrow-shaped microneedles were fabricated in ways that attributed different properties to the multi-roof structures. The shape and surface morphology of the final structures were investigated by scanning electron microscopy and optical microscopy. Their performance was also investigated using histological analysis and optical investigation after insertion of molded microneedles into tissue. Results show that biodegradable polymeric micro-particles encapsulating chemical compounds were successfully used as filling material into the mold to fabricate multi-compositional structures with various geometries, and all from a single micromold. We conclude that this novel micromolding technique should facilitate microreplication of polymer microstructures with complex geometries and compositions.
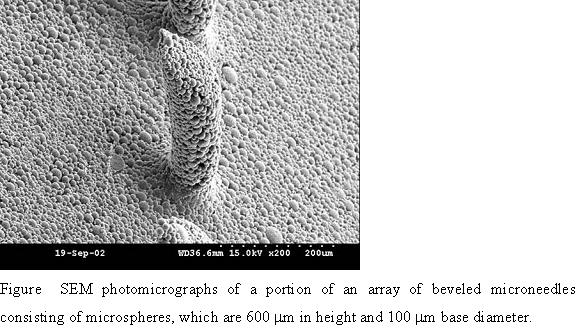